An intelligent fleet for the Audi A8
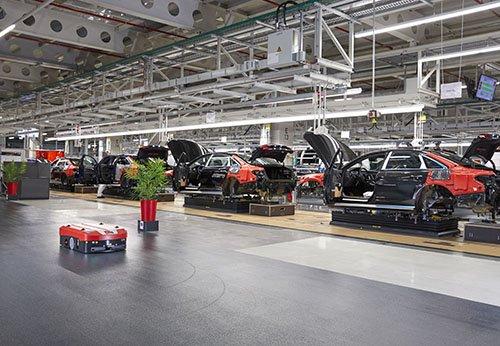
Breaking News:
Freitag, Apr 26, 2024
Right of way for intelligent system solutions: For the manufacturing of the new Audi A8 in Neckarsulm, the Grenzebach Group incorporates a system solution with 30 L1200S Automated Guided Vehicles (AGVs) for high-performance process networking. “Automated Guided Vehicles that are driven by the concept of an intelligent fleet forms the core of intralogistics in a smart factory“, says Uwe Dopf, Head of Business Unit Intralogistics at the Grenzebach Group.
At the Neckarsulm Audi plant, the AGVs supply mounting parts to production workers and assembly robots at flexible manufacturing islands. The Grenzebach Fleet Manager navigates the vehicles via optimal transport routes. The Fleet Manager receives the transport orders from various positions: from bar code scanners at the parts location, from manually operated rockers at the installation location, from robot cells with filling level control of the goods carriers as well as from Audi’s ERP system.
Readily available on optimal transport routes
The 30 Automated Guided Vehicles interact as a fleet. The most economic correlation between the AGV and the transport order is carried out during running production. Thus, the optimal number of vehicles and optimal transport routes for all assignments can be ensured. Furthermore, fleet interaction guarantees availability – an AGV can accept orders from another vehicle should that lead to improvement of the overall performance.
Different band speeds and flexible assembly sequences: The fleet of L1200S AGVs contributes to production at maximum flexibility with considerable advantages compared to manual provisioning with tugger trains. This is realized with innovative energy management as the batteries of the AGVs are charged contact-free via inductive charging mats.
Industry 4.0 in practice
Status displays of the different L1200S vehicles, including pending transport orders, are shown in real time with the Fleet Manager. "The processes are open to the interventions of authorized users. Thus, places of provisioning for the AGVs at Audi can be changed during running production", explains the Grenzebach expert Dopf. The Fleet Manager is the control center for Intralogistics. Industry 4.0 in practice: All transport, status and error messages are locally stored and can be evaluated with the customer’s existing systems.
From the container to the car body
The routes between the supply and working stations in the assembly hall A11 at the Audi plant in Neckarsulm occur on three levels – the Automated Guided Vehicles are on their way via elevators in the basement, first floor and the lower floor of the workshop. Sequence vehicles loaded with components are transported automatically with the L1200S moving beneath it from the supply stations to the work station they are requested at. Furthermore, other scopes carrying car-related material (pearl chain process) are provided at the assembly station with an AGV.
The 30 AGVs use contour navigation in the workshop to reach their destination. Certified laser scanners on the vehicle calculate the vehicle’s position by reflection of environment characteristics. Contact loops or other optical means on the shop floor are not necessary.
Docking to a complex environment
The route is redefined by the Grenzebach Fleet Manager, completely intrinsically safe – this is also ensured by the laser scanner. With the integrated personal security sensor technology, the L1200S vehicle can be used in plant-internal environments. Due to its free contour guidance, protected zones are obsolete, saving floor space and allowing for simple integration into existing environments. Thus, the L1200S can be used in its most optimal way for mixed operation with conventional tugger trains and on elevators. The customer-specific guidelines of the Audi AG for increased employee safety are perfectly met with the 30 AGVs. For mixed operation with conventional tugger trains, Audi and Grenzebach elaborate separate rules of conduct. ”The use for the A8 production shows that a system solution with the smart AGV can be integrated into a complex environment at any time“, says Uwe Dopf. The fleet of L1200S AGVs was integrated simultaneously for the manufacturing of two Audi A8 models (predecessor model D4, new model D5) across a 2-shift production.
The L1200S routes in detail
In a simplified representation, this is how the L1200S vehicles navigate at the Neckarsulm Audi plant. Parts supply by employees: The Audi employees put the readily commissioned sequence vehicles into a fixed transfer area. The AGV moves beneath the container and starts to travel towards the place of provision; this position can be changed by the Fleet Manager during running production! The empty sequence vehicles are placed onto a defined surface by the AGV. En route at the plant: On the ground floor, the AGV picks its optimal route within the 5 meters wide main traveling paths and on secondary paths with a width of at least 3.5 meters. On the upper floor, the paths are also 5 meters wide; however, at the cockpit level they are reduced to 3.4 meters. The travel paths are used by the L1200S AGVs together with manual tractor vehicles and stackers. Oncoming traffic can occur anywhere on the route. Employees also travel in the same area as the vehicles. The AGV moves between the different floors with freight elevators – These communicate with the AGV via a field-bus interface. Exchange at the manufacturing cell: The transport vehicles are available at the assembly location following the two-container principle. When a container is empty, it is removed by the AGV. After that, the AGV supplies a full container and makes it available to the system.
The small, flexible L1200S vehicles, which are able to turn on the spot and can navigate within a room with sensors, are perfectly suited for automatic transportation of material and components. Strong, mobile, flexible and safe! And thanks to the Fleet Manager they are intelligent and self-learning on their way. In the A8 production at Neckarsulm, the celebrity of the Grenzebach Intralogistics can show their strengths.
More information:
Grenzebach Group
Albanusstrasse 1
86663 Asbach-Bäumenheim
Telefon: +49 (906) 982-2000
Telefax: +49 (906) 982-108
http://www.grenzebach.com/de/