The Complete Guide to Smart Factories
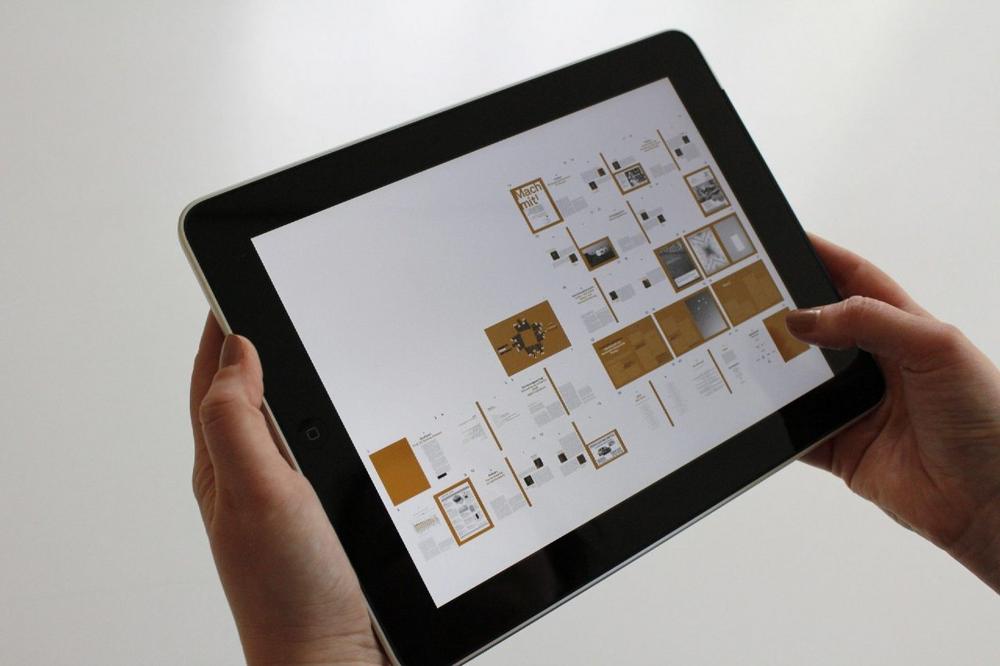
Breaking News:
Business-Software-Anbieter KUMAVISION baut Partnermanagement aus
Nicht nur für Überflieger und Einserkandidaten: Tipps aus erster Hand beim „Tag des Stipendiums“
Worauf sollte ein Schuldner bei einer Schuldnerberatungsstelle unbedingt achten?
Die unterschätzten Möglichkeiten der eigenen Website für Content Creators
Freitag, Mai 3, 2024
The meeting of technology and the virtual world with the real world allows the smart factory to make an impact now rather than in the future. The integration of different artificial intelligence, algorithmic learning, the automation of transportation, and machine learning within a manufacturing process is making this possible. The emergence of the smart factory and industry 4.0 will fundamentally change how products are manufactured, shipped, and delivered to consumers. But this will also lead to improved worker safety, protection from the reliance on human resources (COVID-19 as the prime example here), and hopefully a reduction in harmful emissions. Machines’ ability to begin communicating with each other in a smart ecosystem will lead to literally “smart” manufacturing facilities. This guide will outline what a smart factory is, what technology is driving this movement, and the implementation may look like.
What is a smart factory?
Essentially a smart factory has become possible because of the advancements in how data is being handled, now commonly referred to as “Big Data.” Fundamentally a smart factory is a facility where the machinery inside is linked/connected. This then allows the industrial equipment to react, learn, and adapt their processes leading to a “smart factory.” The ability to handle large amounts of complex data that is passed through the machinery has paved the way for the smart factory’s arrival. A smart factory will connect industrial internet connections to connect to the cloud, which bridges the online and physical worlds.
Using machinery or add-on devices that can communicate with each other in a cohesive language leads to many potential improvements. It can lead to maintenance feedback, which prevents breakdowns and stoppages in the assembly line. It can also lead to a much more flexible production line allowing the different machinery to work together.
What led to the rise of the smart factory?
Soon the separated and siloed machinery within manufacturing facilities will be a thing of the past. Smart factories will open a full ecosystem allowing machinery from different sectors to provide data that leads to a functional smart factory smoothly. But what technological developments have allowed these developments to occur. The first of these developments has been the introduction of 5G and industrial internet connections.
The development of these strengthened internet connections means that there will be better downloading and uploading capacities. On top of this, the development of lower latency and the ability to manage a more significant number of applications simultaneously. This last point is particularly essential within the manufacturing industry and the rise of smart factories.
The next development in technology is automation and robotics; the outcomes in these areas has improved dramatically. The navigation ability in different AGVs (automated guided vehicles) and AMRs (automated mobile robots) has developed and become cheaper, leading to greater use of natural navigation within manufacturing facilities. These AGVs and AMRs can be hooked up via the industrial internet connections to a fleet management system leading to analytics and data on how materials are transported. This data can be used to adapt and improve the transportation processes leading to great leaps in productivity and efficiency.
FlexQube’s eQart has been developed as a first step into the automation world by creating a user-friendly and easy to implement AGV. The eQart also keeps the original DNA of the FlexQube concept, which leads to the world’s most flexible AGV on the market.
The emergence of machine to machine communication with the Internet of Things (IoT) also adds to the smart factory’s development. The addition of sensors, software, and other technology has really improved the way that heavy manufacturing machinery can communicate with each other. This communication between machinery is key to the flow of processes within a smart factory. Having these machines speak and communicate allows for significant improvements in efficiency, safety, and productivity.
Some other advancements in technology that makes the smart factory possible are:
Implementing a smart factory
According to Deloitte in their 2020, “Implementing the smart factory: New perspectives for driving value,” 86% of manufacturers believe that smart factories will be the primary driver of competition by 2025, and 83% believe that smart factories will transform the way that products are made. This is a significant number of manufacturers that see smart factories as the way of the future; however, taking the first steps towards implementation can be difficult. So how does one go about implementing a smart factory? Below we will only outline some general themes that need to be taken into account when undergoing a transition rather than a step by step because every factory is different.
The first theme to take into consideration when undergoing such a transformation is ensuring you understand each task that is needed to be completed within the facility. Knowing what each operator does in their daily duties and knowing how you can make it easier and what information you need to keep track of. By doing this, you can find the concerns that need to be addressed and the behaviors and habits that need to be changed. Just undergoing this investigation can lead to improvements in the process and action.
Secondly, a wide variety of skills and resources will be needed to transition towards a smart factory. Having a diverse range of skills and experience allows for creating a culture of vision and understanding. Standard skillsets that will be needed to undertake a smart factory transformation are engineering, IT, production skills, data management skills, and analytics. Bringing on software engineers and human operators to work together to get the right information collected will be needed. Bringing in these skills to create an ecosystem that can develop a culture of insight and intelligence is essential, but finding ways to create and support this is also important. Finding ways to know who can be grown in your existing staff to take on roles throughout the change is also essential. A culture of support and learning will pay dividends in the future as problem-solving and critical thinking skills grow in demand.
Thirdly, having a focus on connectivity is essential throughout each stage of your smart factory transition. Ensuring that you have the infrastructure that can manage multiple devices, all being connected, is vital. The success of an intelligent factory is all about being able to connect machinery and processes. So without a firm, robust plan around connectivity, it will be difficult to enjoy the full advantages of a smart factory.
Because each factory is different and different products need other processes, the transition to a smart factory can be managed differently. Taking advantage of the new technological advancements available takes a lot of preparation and planning. Having the right team and resources available can make the transition smooth and lead to improvements in safety, efficiency, throughput, and productivity. So getting the transition right can be worth the investment in the long run.
FlexQube offers a unique and patented concept that is used to design and deliver robust, modular and flexible material handling carts that can also run autonomous. The company has manufacturing in Sweden and USA and distribution in North America and in Europe. On December 14, 2017, the company was listed on the Nasdaq First North in Sweden.
FlexQube has some of the world’s largest manufacturers within automotive-, energy-, defense-, aerospace-, home appliances-, and construction machinery among their customers. Some examples are Volvo Cars, Siemens, Autoliv, Scania, Whirlpool, Eberspächer and Mann+Hummel.
FlexQube GmbH
Feldbergstrasse 27-29
61440 Oberursel
Telefon: +49 (160) 2436305
http://www.flexqube.com