Dimensionslose Parameter für das Lasersintern
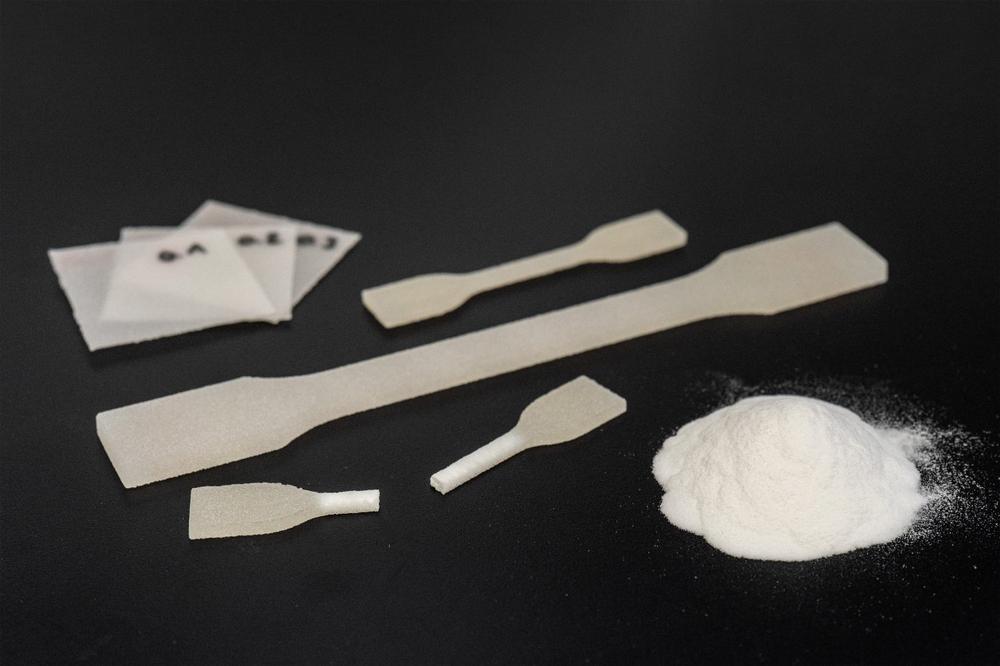
Breaking News:
Mittwoch, Juli 23, 2025
Unter der Leitung von Dr. Johannes Rudloff und in Zusammenarbeit mit Dr. Claas Bierwisch vom Fraunhofer-Institut für Werkstoffmechanik IWM konnte der in der ersten Projektphase entwickelte Monolayer-Ansatz erfolgreich weiterentwickelt und validiert werden. Die Ergebnisse zeigten eine hohe Übereinstimmung zwischen numerischen Simulationen, Monolayer-Druckversuchen, energetischer Modellierung und den Resultaten aus Mehrschicht-Baujobs mit Polyamid 12 (PA12) und Polypropylen (PP).
Schneller zum optimalen Prozessfenster
Das Lasersintern (PBF-LB/P) zählt zu den wichtigsten Verfahren in der additiven Fertigung von Kunststoffen. Die begrenzte Materialvielfalt bleibt jedoch eine zentrale Herausforderung. Um diese zu adressieren, kombinierte das Projektteam numerische Simulationen mit Material- und Prozessdaten, um die Energieumwandlung im Verfahren anhand dimensionsloser Parameter für PA12- und PP-Pulver zu analysieren.
Durch einfache Monolayer-Druckversuche mit verschiedenen Energieeinträgen und anschließender Dicke-Messungen konnte ein geeignetes Prozessfenster identifiziert werden.
Dieser ressourcensparende Ansatz ermöglicht eine signifikante Zeitersparnis in der Prozessentwicklung. Der optimale Punkt der eingetragenen Oberflächenenergiedichte ist dabei durch den Schnittpunkt der beiden dimensionslosen Kennzahlen für Energieeinbringung und Energiebedarf definiert – also dort, wo ihre Differenz null ist.
Validierung durch mechanische Tests
Zur Verifizierung der prognostizierten Parameter wurden Zugprobekörper gefertigt und mechanisch getestet. Die Ergebnisse bestätigten die Praxistauglichkeit des Ansatzes:
Bei ähnlichen Werten von Energieeinbringung und -bedarf wurden für PA12 und PP die besten mechanischen Eigenschaften erzielt. Dies unterstreicht das Potenzial des Monolayer-Ansatzes als effektives Werkzeug zur schnellen und zuverlässigen Identifikation geeigneter Prozessparameter – auch für neuartige Materialien.
Mehrschichtversuche und Einfluss der Zwischenschichtzeit
Ergänzend wurden Mehrschichtversuche durchgeführt, um den Einfluss der Zwischenschichtzeit (Inter Layer Time, ILT) auf die Bauteileigenschaften zu untersuchen. Die Ergebnisse zeigten eine Zunahme der Dichte bei höheren ILTs – im Einklang mit den Simulationen.
Fazit
Das Projekt leistet einen wesentlichen Beitrag zur Weiterentwicklung des Lasersinterns und zur Integration neuer Materialien in die additive Fertigung. Die entwickelten Methoden ermöglichen eine schnellere, effizientere und wissenschaftlich fundierte Prozessentwicklung – ein wichtiger Impuls für Forschung und Industrie. Weitere geförderte Umsetzungsprojekte befinden sich in Vorbereitung und sollen innerhalb der nächsten sechs Monate starten.
Damit wurde das von der Deutschen Forschungsgemeinschaft (DFG) geförderte Projekt „Numerische und experimentelle Untersuchungen von dimensionslosen Materialparametern in der generativen Fertigung von Polymeren mittels Laser-Sintern – Teil 2: Erweiterung des Anwendungsfelds“ (Förderkennzeichen BA 1841/32-2), das am 01.01.2022 startete und bis zum 30.06.2025 lief, erfolgreich abgeschlossen.
Inklusive des ersten Teilprojekts endet eine fast siebenjährige Förderung. Das Projektziel war es, den Powder Bed Fusion (PBF)-Prozess durch dimensionslose Kennzahlen besser zu beschreiben und so die Parameterfindung für neue Materialien sowie die Prozessoptimierung deutlich zu beschleunigen.
Das SKZ freut sich über Anfragen aus der Industrie zur Anwendung von Simulationen und dimensionslosen Kennzahlen für eine zielgerichtete Materialentwicklung und Prozessauslegung.
Das SKZ ist ein Klimaschutzunternehmen und Mitglied der Zuse-Gemeinschaft. Diese ist ein Verbund unabhängiger, industrienaher Forschungseinrichtungen, die das Ziel verfolgen, die Leistungs- und Wettbewerbsfähigkeit der Industrie, insbesondere des Mittelstandes, durch Innovation und Vernetzung zu verbessern.
FSKZ e. V.
Friedrich-Bergius-Ring 22
97076 Würzburg
Telefon: +49 931 4104-0
https://www.skz.de