Tethered caps: KHS optimizes its inspection technology with the help of artificial intelligence
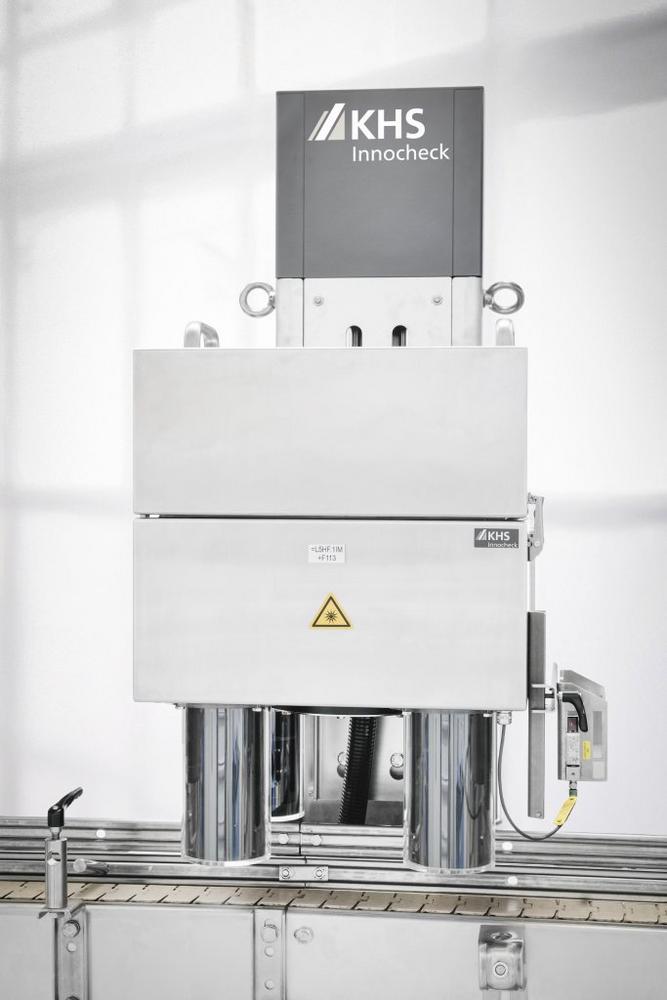
The obligatory introduction of tethered caps had far-reaching consequences for bottle and beverage producers in the EU. They were forced to find new solutions to continue to meet the high demands made of product quality and protection. This also affected inspection technology, explains Nikita Wall from Labeling and Inspection Technology Product Support at KHS. “Tethered caps were rarely used before the EU directive came into force. Conventional systems thus frequently reach the limits of their capacity where cap inspection is concerned.” What’s more, the large number of bottle and cap design variants processed and increasing line capacities present additional challenges.
Optimized cap inspection thanks to AI
With its AI-based fault detection system for tethered caps, the Dortmund turnkey supplier now provides smart engineering that identifies potential defects during cap inspection. The new module makes use of patent-pending algorithms to analyze images of bottle closures in real time. Cameras log the caps in high-resolution quality, while AI models evaluate this data. By applying deep learning, the models adjust to account for any new types of flaw found.
KHS’ AI-assisted system increases both the accuracy and efficiency of inspection. “Our customers make extremely high demands of quality assurance. In intensive field tests, our AI-based fault detector has proved that it fully meets these requirements,” emphasizes Wall.
Foundation for further projects
KHS has developed the new system specifically for its tried-and-tested Innocheck TSI cap inspector. It can be implemented on both new and existing machines.
In the future, KHS also wants to use AI for further inspection technology equipment. Says Wall, “In the development team, we’re currently discussing which systems this would make sense for. AI solutions are only practical where the requirements are complex – and if they give our customers clear benefits.”
For more information go to:
https://www.khs.com/en/company/media
Why not subscribe to our newsletter so that you don’t miss any of the latest news? https://www.khs.com/en/company/media/publications/web-magazine
The KHS Group is one of the world’s leading manufacturers of filling and packaging systems for the beverage and liquid food industries. Besides the parent company (KHS GmbH) the group includes various subsidiaries outside Germany, with production sites in Ahmedabad (India), Waukesha (USA), Zinacantepec (Mexico), São Paulo (Brazil) and Kunshan (China). It also operates numerous sales and service centers worldwide. KHS manufactures modern filling and packaging systems for the high-capacity range at its headquarters in Dortmund, Germany, and at its factories in Bad Kreuznach, Kleve, Worms and Hamburg. The KHS Group is a wholly owned subsidiary of the SDAX-listed Salzgitter AG corporation. In 2024 the KHS Group and its 5,626 employees achieved a turnover of around €1.654 billion.
KHS GmbH
Juchostr. 20
44143 Dortmund
Telefon: +49 (231) 569-0
Telefax: +49 (231) 569-1541
http://www.khs.com